The Scientific Research Behind Porosity: A Comprehensive Guide for Welders and Fabricators
Understanding the intricate mechanisms behind porosity in welding is critical for welders and fabricators pursuing impressive craftsmanship. As metalworkers look into the midsts of this phenomenon, they reveal a globe regulated by numerous factors that affect the formation of these small gaps within welds. From the composition of the base materials to the ins and outs of the welding process itself, a multitude of variables conspire to either intensify or relieve the presence of porosity. In this thorough guide, we will certainly untangle the science behind porosity, discovering its results on weld quality and introduction advanced strategies for its control. Join us on this journey with the microcosm of welding flaws, where precision satisfies understanding in the quest of remarkable welds.
Understanding Porosity in Welding
FIRST SENTENCE:
Exam of porosity in welding discloses important understandings into the honesty and high quality of the weld joint. Porosity, identified by the presence of cavities or voids within the weld metal, is an usual worry in welding procedures. These spaces, if not correctly addressed, can compromise the architectural integrity and mechanical residential properties of the weld, bring about potential failings in the finished product.
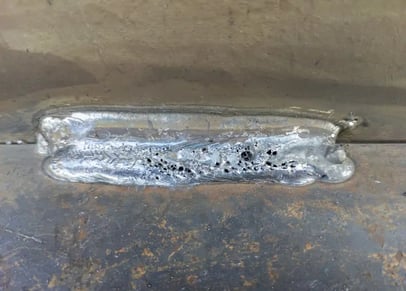
To find and evaluate porosity, non-destructive testing approaches such as ultrasonic testing or X-ray evaluation are often utilized. These strategies permit for the identification of internal defects without jeopardizing the integrity of the weld. By evaluating the dimension, shape, and circulation of porosity within a weld, welders can make enlightened decisions to boost their welding processes and achieve sounder weld joints.
Aspects Affecting Porosity Formation
The occurrence of porosity in welding is influenced by a myriad of aspects, varying from gas protecting efficiency to the intricacies of welding parameter settings. Welding criteria, consisting of voltage, present, travel speed, and electrode kind, also influence porosity formation. The welding method employed, such as gas metal arc welding (GMAW) or protected steel arc welding (SMAW), can affect porosity development due to variants in warm distribution and gas insurance coverage - What is Porosity.
Results of Porosity on Weld High Quality
The presence of porosity also deteriorates the weld's web resistance to corrosion, as discover this info here the trapped air or gases within the gaps can react with the surrounding setting, leading to destruction over time. In addition, porosity can hinder the weld's ability to endure stress or impact, additional jeopardizing the overall top quality and reliability of the bonded framework. In vital applications such as aerospace, automobile, or architectural constructions, where security and resilience are paramount, the destructive impacts of porosity on weld high quality can have severe repercussions, stressing the importance of minimizing porosity with correct welding techniques and treatments.
Methods to Decrease Porosity
To enhance the high quality of bonded joints and ensure architectural integrity, welders and fabricators employ particular techniques aimed at lowering the development of gaps and cavities within the material during the welding process. One effective method to lessen helpful hints porosity is to make certain appropriate product prep work. This consists of complete cleaning of the base steel to eliminate any impurities such as oil, grease, or moisture that can contribute to porosity development. Additionally, using the ideal welding parameters, such as the proper voltage, existing, and take a trip speed, is vital in stopping porosity. Maintaining a constant arc length and angle during welding likewise aids reduce the probability of porosity.

Using the appropriate welding technique, such as back-stepping or utilizing a weaving motion, can also help distribute heat evenly and reduce the chances of porosity development. By carrying out these techniques, welders can properly reduce porosity and create top notch welded joints.
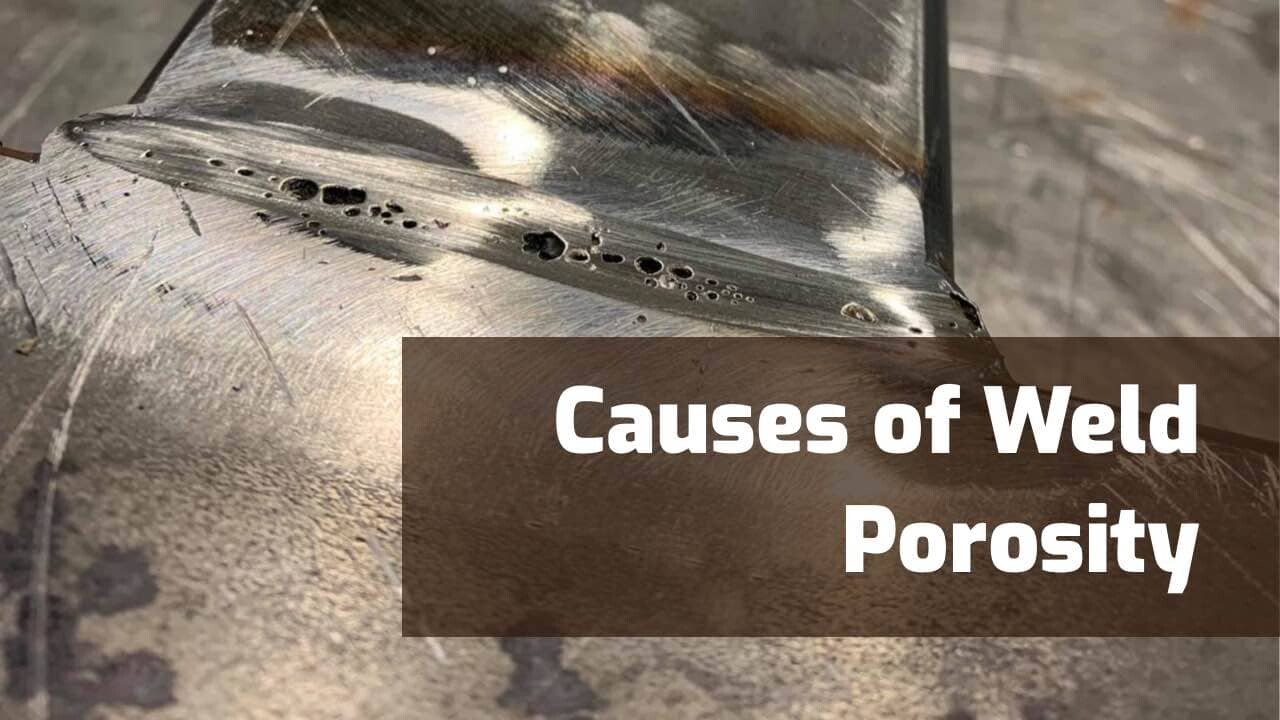
Advanced Solutions for Porosity Control
Carrying out innovative modern technologies and ingenious methods plays a crucial function in achieving premium control over porosity in welding processes. One sophisticated remedy is making use of innovative gas mixes. Protecting gases like helium or a mix of argon and hydrogen can help in reducing porosity by giving far better arc stability and enhanced gas coverage. Additionally, using advanced welding methods such as pulsed MIG welding or customized ambience welding can likewise help alleviate porosity problems.
An additional sophisticated service includes making use of sophisticated welding equipment. Making use of tools with built-in features like waveform control and sophisticated power resources can boost weld top quality and reduce porosity threats. Moreover, the implementation of automated welding systems with specific control over specifications can dramatically reduce porosity flaws.
Furthermore, incorporating sophisticated monitoring and assessment technologies such as real-time X-ray imaging or automated ultrasonic screening can help in spotting porosity early in the welding procedure, enabling immediate corrective actions. Overall, incorporating these advanced options can greatly enhance porosity control and enhance the general high quality of welded parts.
Verdict
In conclusion, recognizing the scientific research behind porosity in welding is essential for welders and producers to create top notch welds - What is Porosity. Advanced services for porosity control can better improve the welding procedure and make sure a solid and trustworthy weld.
Comments on “What is Porosity in Welding: Ideal Practices for Preventing Porous Welds”